Parts of a Forklift and Their Function: 5 Critical Components
Forklifts do more than just lift—they impact efficiency and safety. The difference between a counterbalance forklift with a triplex mast and a reach truck with a quad mast isn’t just jargon—it’s thousands in costs and potential risks.
This guide breaks down the parts of a forklift and their functions, from hydraulic systems to mast configurations, cutting through the marketing to show their real-world impact.
Key parts of a forklift include the mast (lifts and lowers loads), forks (support the load), carriage (holds the forks), overhead guard (protects the operator), counterweight (balances the load), and tires (enable movement). Each part works together for safe and efficient lifting.
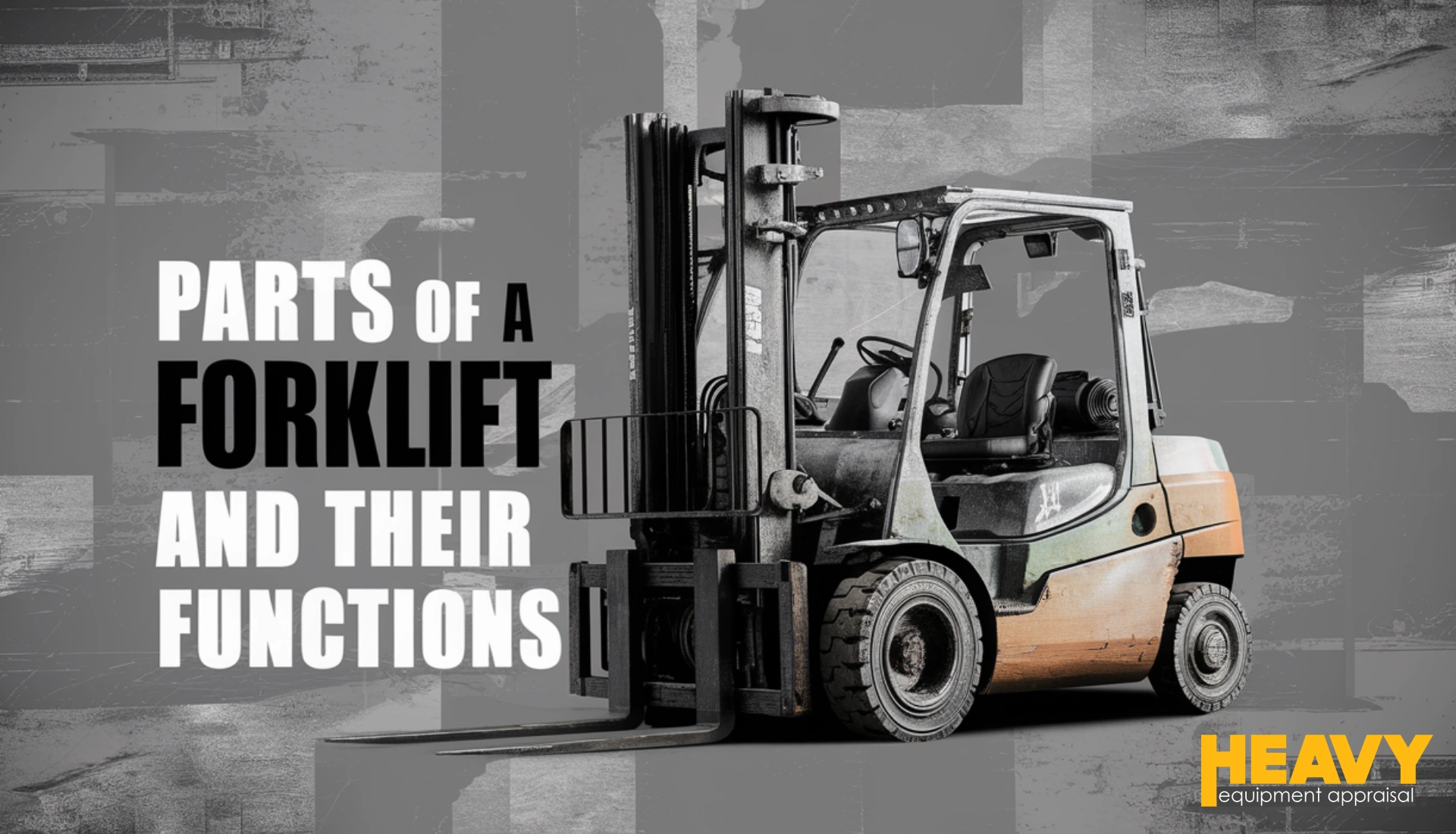
1. Chassis
The chassis is the base frame of a forklift and serves as the foundation for all other components. Think of it as the forklift's skeleton – everything else hangs off this critical structure.
It typically consists of the following parts:
Counterweight
A heavy mass located at the rear of the forklift, the counterweight provides stability by counterbalancing the weight of the load being lifted. It prevents the forklift from tipping forward when carrying heavy loads.
The counterweight plays a critical role in forklift safety by preventing tipovers, which can cause serious injuries and damage. Counterweights can be made of cast iron, concrete, or lead, and their size varies depending on the forklift's lifting capacity.
Engine/Battery Compartment
This compartment houses the forklift's power source. Internal combustion (IC) forklifts have engines that run on gasoline, diesel, or propane, while electric forklifts have (expensive) batteries. The location of the engine or battery compartment can vary depending on the forklift's design.
Operator Compartment
This is where the operator sits and controls the forklift. It includes the seat, steering wheel, pedals, levers, and instrument panel. The cab is the central part of the forklift and houses the steering wheel, brake and gas pedals, mast controls, and gauges. It is also where the safety devices are located.
The operator compartment also contains the controls for driving the forklift and manipulating the load. These include the steering wheel, accelerator and brake pedals, and levers for controlling the lifting, lowering, and tilting of the forks. The operator compartment may be open or enclosed, depending on the working environment and safety requirements.
Wheels and Tires
Forklifts have two types of wheels: drive wheels and steer wheels. Drive wheels, located on the front axle, provide power for movement, while steer wheels, located at the rear, enable steering and maneuverability. Different types of tires are used depending on the operating environment.
Cushion tires are used indoors on smooth surfaces, while pneumatic tires are used outdoors on rough terrain.
Nameplate
Forklifts also have a nameplate that displays important information about the machine's capabilities, such as load capacity and lift height.
2. Mast
The mast is the vertical structure at the front of the forklift that lifts and lowers the load. It consists of interlocking rails and is powered by hydraulic cylinders.
flowchart TD title["Forklift Mast Types Comparison"] style title fill:#f9f9f9,stroke:#333,stroke-width:1px title --> Simplex title --> Duplex title --> Triplex title --> Quad Simplex --> S_Desc["Single-stage mast Lowest lift height Best for outdoors or low clearance"] style S_Desc fill:#e6f7ff,stroke:#333,stroke-width:1px,border-radius:5px Duplex --> D_Desc["Two-stage mast Higher reach Free lift in outer section Good for loading/unloading trailers"] style D_Desc fill:#e6ffe6,stroke:#333,stroke-width:1px,border-radius:5px Triplex --> T_Desc["Three-stage mast Highest common reach Free lift + inner sections Common in warehouses"] style T_Desc fill:#ffe6e6,stroke:#333,stroke-width:1px,border-radius:5px Quad --> Q_Desc["Four-stage mast Extreme heights Shorter collapsed height Specialized applications"] style Q_Desc fill:#f9f0ff,stroke:#333,stroke-width:1px,border-radius:5px classDef default fill:#f9f9f9,stroke:#333,stroke-width:1px,color:#333 classDef heading fill:#f0f0f0,stroke:#333,stroke-width:2px,color:#333,font-weight:bold class title heading class Simplex,Duplex,Triplex,Quad default
Ever wonder why some forklifts can reach higher than others? It's all about the mast design. Different types of masts offer varying lift heights and capabilities:
Simplex
A single-stage mast with the lowest lift height, best for outdoor applications or environments with limited vertical space.
Duplex
A two-stage mast with a higher reach than a simplex mast. It has two sections, outer and inner, with the outer section offering free lift and the inner section elevating the forks and carriage. Duplex masts are suitable for loading and unloading trailers.
Triplex
A three-stage mast providing the highest reach among the common types. It has outer sections for free lift and inner sections for lifting or elevation, generally offering a greater lift height than the two-stage mast. Triplex masts are commonly used in general warehouse applications.
Quad
A four-stage mast suitable for extremely high stacking while maintaining a shorter collapsed height compared to the other mast types.
3. Carriage and Forks
The carriage is a platform attached to the mast that holds the forks. It moves up and down along the mast and can also tilt forward and backward to stabilize the load.
The forks are the two long, parallel prongs that slide under the load and lift it. Forklift forks come in different sizes, are made of strong steel and can be adjusted to fit different load sizes.
4. Hydraulic System
The hydraulic system is responsible for lifting and lowering the load, as well as tilting the mast and carriage. It consists of hydraulic cylinders, pumps, and control valves. The hydraulic lift cylinder raises and lowers the forks, while the tilt cylinder allows the mast to tilt forward or backward.
5. Power Source
Forklifts can be powered by either internal combustion engines or electric motors:
Internal Combustion Engines
These engines run on gasoline, diesel, or propane and are typically used in outdoor applications or where greater power is required.
Electric Motors
Electric forklifts use rechargeable batteries and are preferred for indoor use due to their zero emissions and quiet operation. Electric forklifts utilize different battery types, each with its own performance characteristics.
Lead-acid batteries are a common and cost-effective option, while lithium-ion batteries offer higher energy density, faster charging times, and longer lifespans. The choice of battery depends on factors such as usage patterns, required runtime, and budget.
Powertrain
The powertrain of a forklift encompasses the components that generate and transmit power for lifting and moving. This includes the power source (engine or battery), transmission, hydraulic pump, lift cylinder, tilt cylinder, and lifting chain. The transmission works in conjunction with the power source to control speed and direction.
The hydraulic pump powers the lift and tilt functions by moving hydraulic fluid through the system. The lift and tilt cylinders enable the mast to raise, lower, and tilt, while the lifting chain facilitates the vertical movement of the carriage and forks.
Safety Features
Forklifts are equipped with various safety features to protect the operator and those working nearby.
flowchart TB classDef featureBox fill:#f0f8ff,stroke:#336699,stroke-width:2px,color:#333,font-weight:bold classDef functionBox fill:#fff8f0,stroke:#996633,stroke-width:1px,color:#333 classDef benefitBox fill:#f0fff8,stroke:#339966,stroke-width:1px,color:#333,font-style:italic MainTitle["Forklift Safety Features & Their Functions"] style MainTitle fill:#f5f5f5,stroke:#333,stroke-width:1px,font-weight:bold MainTitle --> OperatorProtection MainTitle --> VisibilityFeatures MainTitle --> StabilityControls MainTitle --> WarningDevices MainTitle --> SmartSafety %% Operator Protection Group OperatorProtection["Operator Protection Features"] class OperatorProtection featureBox OperatorProtection --> OverheadGuard["Overhead Guard"] OverheadGuard --> OG_Function["Protects operator from falling objects"] OG_Function --> OG_Benefit["Reduces risk of severe injury by up to 80%"] OperatorProtection --> SeatBelt["Seat Belt/Operator Restraint"] SeatBelt --> SB_Function["Keeps operator inside cab during tip-over"] SB_Function --> SB_Benefit["Critical in tipping incidents - prevents crushing"] OperatorProtection --> LoadBackrest["Load Backrest Extension"] LoadBackrest --> LB_Function["Prevents load from shifting toward operator"] %% Visibility Features VisibilityFeatures["Visibility Enhancement"] class VisibilityFeatures featureBox VisibilityFeatures --> Lights["Safety Lights"] Lights --> Lights_Function["Blue spot lights, strobe lights, headlights"] Lights_Function --> Lights_Benefit["Reduces collision rates by up to 60%"] VisibilityFeatures --> Mirrors["Mirrors & Cameras"] Mirrors --> Mirrors_Function["Improves visibility for blind spots"] %% Stability Controls StabilityControls["Stability Systems"] class StabilityControls featureBox StabilityControls --> LSC["Load Stability Control"] LSC --> LSC_Function["Monitors mast angle & limits functions when unsafe"] StabilityControls --> SCS["Stability Control System"] SCS --> SCS_Function["Adjusts speed based on load height & turning angle"] SCS_Function --> SCS_Benefit["Prevents most common tip-over scenarios"] %% Warning Devices WarningDevices["Warning Devices"] class WarningDevices featureBox WarningDevices --> BackupAlarm["Backup Alarm"] BackupAlarm --> BA_Function["Audible warning when reversing"] WarningDevices --> Horn["Horn"] Horn --> Horn_Function["Manual warning at intersections"] %% Smart Safety SmartSafety["Smart Safety Technology"] class SmartSafety featureBox SmartSafety --> ProximitySensors["Proximity Sensors"] ProximitySensors --> PS_Function["Detects pedestrians/obstacles & alerts driver"] PS_Function --> PS_Benefit["Reduces collision incidents by up to 75%"] SmartSafety --> SpeedZoning["Automatic Speed Zoning"] SpeedZoning --> SZ_Function["Auto-reduces speed in designated areas"] SmartSafety --> AccessControl["Operator Access Control"] AccessControl --> AC_Function["Prevents unauthorized usage"] AC_Function --> AC_Benefit["Electronic checklist enforces pre-operation inspections"] %% Apply classes class OG_Function,SB_Function,LB_Function,Lights_Function,Mirrors_Function,LSC_Function,SCS_Function,BA_Function,Horn_Function,PS_Function,SZ_Function,AC_Function functionBox class OG_Benefit,SB_Benefit,Lights_Benefit,SCS_Benefit,PS_Benefit,AC_Benefit benefitBox
Examples of safety devices include seat belts to secure the operator, overhead guards to protect from falling objects, and alarms to alert pedestrians and other workers. Some key safety features include:
- Overhead Guard: A metal frame above the operator's head that protects them from falling objects.
- Load Backrest: Prevents the load from shifting backward and falling towards the operator.
- Seat Belt: Ensures the operator remains securely seated in the cab.
- Safety Lights and Horns: Provide visibility and audible warnings to alert others of the forklift's presence.
Forklift Safety
Forklift accidents are a significant concern, and understanding their causes is crucial for prevention. Common causes include operator inattention (fatigue, distraction, carelessness), inadequate training, lack of warning signs and signals, improper load creation, speeding, mechanical failures (worn brakes, leaks, damaged tires), and poor workplace design.
According to the U.S. Bureau of Labor Statistics, OSHA, NIOSH, and the National Safety Council, forklift accidents are a significant cause of workplace injuries and fatalities. Every year, numerous accidents occur, resulting in fatalities and injuries. A significant portion of these accidents involve pedestrians.
Operator training is paramount in forklift safety. Properly trained operators are more aware of potential hazards, understand safe operating procedures, and can react effectively in emergencies, significantly reducing the risk of accidents. The Occupational Safety and Health Administration (OSHA) has established standards for powered industrial trucks, including forklifts (29 CFR 1910.178).
These standards address various aspects of forklift safety, including operator training, maintenance, and workplace design. Adhering to these standards is crucial for minimizing risks and ensuring a safe working environment.
Costs
The cost of a forklift varies depending on several factors, including type, capacity, features, and whether it is new or used.
New Forklift Cost Comparison
New Forklifts
New forklifts can range in price from $20,000 to over $45,000, depending on the type and features.
- Electric forklifts: $20,000 to $35,000, plus $2,500 to $5,000 for battery and charger.
- Internal combustion forklifts: $25,000 to $45,000.
- High-capacity forklifts (e.g., 35,000 lbs or more): Can exceed $100,000.
- Specialized models like telehandlers: $65,000 to $130,000.
Reach trucks, designed for narrow aisles and high stacking, typically have a weight range of 3,000 to 5,500 lbs and cost between $30,000 and $55,000 when new. They are commonly used in high-density warehouses and distribution centers.
Forklift Type | Cost Range |
---|---|
Standard Counterbalance Forklifts (3,000-6,500 lbs capacity) | $20,000 - $45,000 |
High-Capacity Forklifts (10,000+ lbs) | $60,000 - $100,000+ |
Electric Reach Trucks | $30,000 - $55,000 |
Specialized models (e.g., telehandlers) | $65,000 - $130,000+ |
Used Forklifts
Used forklifts can be a more affordable option, with prices ranging from $5,000 to $30,000. The price of a used forklift depends on factors such as age, condition, and usage hours.
Rental Costs
Renting a forklift can be a good option for short-term needs or for businesses that do not want to commit to purchasing a forklift.
- Daily rental rates: $150 to $500.
- Monthly rental rates: $1,150 to $4,368.
In addition to the initial purchase price, there are ongoing costs associated with owning and operating a forklift, such as maintenance, fuel, insurance, and operator training.
Performance Metrics
Several key performance indicators (KPIs) are used to measure the efficiency and effectiveness of forklifts:
- Utilization Rate: The percentage of time a forklift is in use.
- Maintenance Costs: The cost of maintaining and repairing a forklift.
- Fuel Consumption: The amount of fuel consumed by a forklift.
- Safety Incidents: The number of accidents or near misses involving a forklift.
Tracking these KPIs allows businesses to identify areas for improvement, such as reducing idle time, optimizing maintenance schedules, and promoting fuel-efficient driving practices. This can lead to significant cost savings and increased operational efficiency.
Usage Rates
Forklifts are used in a wide range of industries, with varying usage rates depending on the sector. Some of the most common industries that utilize forklifts include:
Forklift Usage Rates by Industry
Data based on industry analysis from Electroiq and Straits Research
Retail and e-commerce: This sector is a significant consumer of forklifts, with usage rates projected to increase significantly in the coming years.
Construction: Forklifts play a vital role in moving materials on construction sites. It's important to note that forklift usage carries inherent risks, with construction, agriculture, forestry, and fishing being the sectors with the highest fatality rates, accounting for 65% of forklift-related deaths.
Manufacturing: Forklifts are essential for handling raw materials, moving products between production stages, and managing finished goods.
Warehousing: Forklifts are used extensively in warehouses for loading and unloading trucks, moving pallets, and storing goods.
The projected growth in forklift usage reflects the increasing demand for efficient material handling solutions across various industries. As businesses strive to improve productivity and streamline operations, the reliance on forklifts is expected to continue to rise.
Conclusion
Forklifts aren’t just tools—they’re the unsung heroes of industry, driving productivity from warehouses to construction sites. Understanding each component—counterweights, mast types, and power systems—isn’t just technical trivia; it’s the key to efficiency and avoiding costly downtime.
Safety remains a major concern. The statistics don’t lie—these powerful machines demand respect, proper training, and strict adherence to protocols. Smart businesses invest in training and safety features, reducing accidents, improving productivity, and cutting insurance costs.
As technology advances, forklifts are becoming smarter, cleaner, and more efficient. Electric models are gaining ground, tracking systems optimize fleet usage, and automation is on the rise. Businesses that make informed decisions on selection, maintenance, and operation will maximize their investment and stay ahead in an increasingly demanding market.
FAQ
What are the parts of a forklift and their functions?
The main parts of a forklift include the mast, which lifts and lowers loads; the forks (or tynes), which carry loads; the truck frame, providing structural integrity; and the counterweight, ensuring stability. Other components include the lift cylinder for vertical movement, tilt cylinder for mast angle adjustment, and overhead guard to protect operators from falling objects. The operator cab houses controls for safe operation.
What are forklift prongs called?
Forklift prongs are called "tines," designed to slide beneath loads for lifting and transport. Tines vary in length and thickness depending on the forklift’s load capacity and intended use.
What are the 3 levers on a forklift?
The three primary levers on a forklift control lifting and lowering, mast tilting forward or backward, and side-to-side movement of the forks. These levers enable precise handling of loads.
Which of the following are components of a forklift?
Key components include the mast, forks (tines), carriage, counterweight, overhead guard, and hydraulic controls. These elements ensure stability, load management, and operator safety during material handling.