Choosing the Best Wheel Loader: Beyond Bucket Size & Horsepower
Contrary to what most equipment sales reps push, raw bucket capacity and horsepower aren’t what separate exceptional wheel loaders from expensive disappointments in 2024. Real-world performance depends on application-specific engineering, not just size class. The John Deere 324 P-Tier’s Articulation Plus steering system and Volvo L90H’s load-sensing hydraulics prove that thoughtful design determines whether a $200K investment actually moves material efficiently for a particular operation, whether in quarries, construction sites, or agricultural settings.
This analysis highlights what truly sets the best wheel loaders apart, cutting through manufacturer claims to assess real-world performance across industries.
The best wheel loaders are the Caterpillar 950M, Volvo L120H, Komatsu WA480-8, and John Deere 744L. These models offer excellent reliability, fuel efficiency, operator comfort, and high load capacity. They are widely used in construction, agriculture, and mining for their performance and durability.
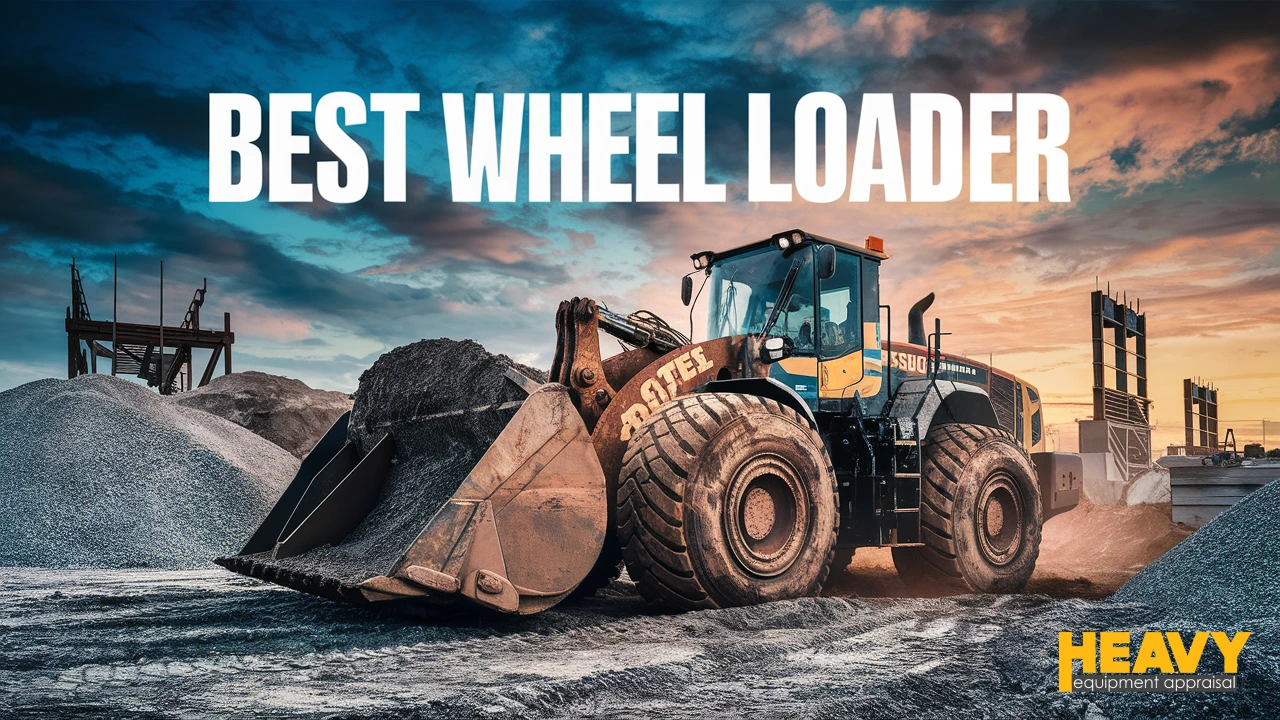
Understanding the Role of Wheel Loaders
Ever watch a wheel loader in action and think, "that's just a tractor with a big spoon on front"? That's like calling a smartphone "just a telephone" - you're missing about 90% of what makes it special.
These machines are the ultimate material handling multi-tools across practically every heavy industry. In construction, they're the first machines on site and the last to leave - moving dirt one day, placing pipe the next, then loading out demolition debris when the project's done.
Talk to any site super about their most versatile machine, and odds are good they'll point to their loader.
In mining and quarrying, larger loaders play the critical role of "keeping the trucks fed" - because an idle haul truck is basically a six-figure paperweight. They move overburden, handle extracted ore, and keep the entire operation flowing. Downtime isn't just inconvenient here; it's catastrophically expensive.
Agriculture has embraced loaders for everything from mundane feed handling to managing massive hay bales that would require a small army to move manually. Ever see those massive round bales stacked five high in a barn? Thank a wheel loader for that.
But they don't stop there. Visit a landscape supply yard and you'll see them loading mulch and topsoil with balletic precision. Waste transfer stations rely on them to handle materials nobody wants to touch manually. Lumber yards use them to move stacks of timber that would make Paul Bunyan think twice.
Sizing is where the decision-making gets interesting. Compact loaders give you that "knife through butter" maneuverability in tight spaces where anything larger would be like performing surgery with boxing gloves.
Mid-size machines hit that Goldilocks zone of capability-to-cost ratio for general contractors. And those large loaders? They're purpose-built material-moving monsters for operations measured in tons per hour rather than buckets per day.
Buying the right loader isn't just about maximum bucket size or sticker price.
Smart operators focus on the full picture: performance metrics that match your daily requirements, fuel burn that won't eat your profit margins, durability that keeps it working when lesser machines are in the shop, and application-specific features that might seem like luxuries until you realize they're cutting 20% off your cycle times.
The Leading Players: Top Wheel Loader Manufacturers in the US Market
The wheel loader market isn't exactly a crowded field - it's more like a heavyweight boxing division where a handful of contenders command most of the attention while smaller fighters try to land the occasional upset.
The usual suspects include Caterpillar, Komatsu, CNH Industrial (that's Case and New Holland for those who don't speak corporate merger), JCB, Volvo CE, Hitachi, SANY, Liebherr, and Deere & Company.
Hyundai and Manitou hover around the edges, throwing occasional haymakers in specific weight classes.
Let's talk market share - the numbers tell a story that sales brochures never will. Cat, Volvo CE, and Komatsu collectively control nearly a quarter of the total wheel loader pie. Not quite monopoly territory, but enough market power to make smaller players nervous.
Looking at recent financing data through July 2024, Caterpillar leads with 21.6% of financed new sales, with Deere surprisingly close at 19.8%, and Komatsu holding steady at 13.4%.
Remember that these numbers shift depending on who's measuring and how - but they give us a solid picture of who's moving metal.
The used market? That's a different animal entirely. Cat dominates even more decisively there with 28.6% of financed used sales. Deere comes in at 22.7%, and interestingly, Case pulls a stronger 14.7% in used than they manage in new sales.
This suggests either impressive durability keeping their older machines in demand (likely) or pricing that's particularly attractive in the secondary market (also likely).
Looking at used sales value in mid-2024, Cat's $630 million utterly dwarfs the competition - with Case at $146 million, Komatsu at $105.6 million, and Volvo and Deere trailing at $50.4 million and $42.8 million respectively.
That massive Cat value lead isn't just about premium pricing - it's also about the sheer volume of yellow iron circulating in the field.
These manufacturers aren't exactly resting on their laurels either. Deere launched their 444 G-Tier and 326 P-Tier telescopic compact loaders in January 2024, Case expanded their compact lineup in October 2023, and Cat introduced the 995 in mid-2023 while refreshing their medium loaders and compact track/skid steer lineup.
Bobcat scored industry cred when their L95 compact made Construction Equipment's "Top 100 New Products" list - an accolade that actually matters to buyers who do their homework.
Meanwhile, Komatsu rolled out new WA700-8 and WA475-10 models, Volvo doubled down on electric loader manufacturing while updating their L180H and L120H conventional models, and Hyundai crashed the party with their high-capacity HL985A in March 2023.
This flurry of activity isn't just about press releases and trade show buzz - it's evidence of fierce competition in a market where standing still means getting lapped.
Manufacturers are pushing hard on performance, sustainability, and specialized capabilities because customers are increasingly sophisticated about what moves their bottom line.
Model Spotlight: In-Depth Analysis of the Best Wheel Loaders
Let's cut through the marketing fluff and look at what's actually worth your attention in the 2024 loader lineup.
Model | Category | Engine Power (hp) | Operating Weight (lbs) | Bucket Capacity (cu. yd.) | Price Range ($) | Key Feature |
---|---|---|---|---|---|---|
Compact Wheel Loaders | ||||||
John Deere 324 P-Tier | Compact | 71 | 14,110 | 1.0–2.1 | 103,500-156,100 | Articulation Plus steering system |
Bobcat L95 | Compact | 74 | 11,993 | 1.25-2.0 | 88,900-115,750 | Top 100 New Product of 2024 award |
Volvo L35 | Compact | Not Specified | Not Specified | Not Specified | Not Specified | Exceptional traction for short-cycle loading |
Medium-Sized Wheel Loaders | ||||||
Komatsu WA320-8 | Medium | 165 | 34,128-34,987 | 3.0-4.2 | 137,500-267,000 | Versatile performer for material loading |
Volvo L90H | Medium | 184 | 31,968-38,140 | 2.9-9.2 | 217,600-257,975 | Versatile across agriculture to waste management |
Caterpillar 966H | Medium | 262 | 52,254 | 4.5-5.5 | 18,000-155,000 | Reliable performance in multiple applications |
Large Wheel Loaders | ||||||
Caterpillar 994K | Large | 1,740 | 529,100 | 25-32.5 | Not Specified | High-capacity mining applications |
John Deere 744 X-Tier | Large | 325 | 56,524-59,267 | 5.0-5.85 | Not Specified | E-Drive electric variable transmission |
Here's the straight talk on machines that are earning their keep across different size classes:
Compact Wheel Loaders
John Deere 324 P-Tier
Ever tried parallel parking a standard loader in a space designed for a golf cart? That's where Deere's Articulation Plus steering system shines - delivering a turning radius that'll make you question physics while still handling a 1.0-2.1 cubic yard bucket.
The 71 hp powerplant and 14,110 lb operating weight hit a sweet spot for general contractors who need versatility without excessive bulk. Pricing runs $103,500 to $156,100 depending on options and your dealer relationship.
It's particularly slick at V-pattern truck loading and hay handling - tasks where precision matters as much as power.
Caterpillar 908
Talk to operators who spend 10-hour days in compact loaders, and they'll tell you Cat's redesigned cab is a game-changer - visibility that reduces neck strain and controls that don't require a PhD to master.
The optional high-flow hydraulics and high-lift configuration transform it from "useful" to "indispensable" for contractors juggling multiple applications. That 25 mph road speed option? It's the difference between making money and losing it on snow removal contracts.
Bobcat L95
When Construction Equipment named this to their "Top 100 New Products of 2024," it wasn't just industry politics - this machine delivers. The 1.2 cubic yard bucket and 10.5-foot lift height from a package with 3,981 lbs straight/3,335 lbs articulated capacity hits an operational sweet spot.
The 74 hp engine provides responsive power without excessive fuel burn. At $88,900 to $115,750, it's attracting buyers from landscapers to mid-size contractors who need compact versatility without compact limitations.
Volvo L35
Here's a machine that built its reputation on traction that borders on supernatural - making it the go-to for short-cycle loading where spin-outs cost you money. Waste and recycling facilities particularly love them because they keep working in conditions that would sideline lesser machines.
Yanmar V10
Yanmar's not the first name most contractors mention, but operators consistently praise this model's combination of grunt, reliability, and controls that feel natural from the first hour. It's becoming the secret weapon for landscape yards, municipalities, and contractors who prioritize daily dependability over brand prestige.
Komatsu WA80-5B
Showing up increasingly as the "calculated alternative" to skid steers in operations where wheel loader efficiency outweighs the initial cost advantage of skids. Smart operators doing the math on total operating costs are making the switch.
Medium-Sized Wheel Loaders
Caterpillar 950 GC
Cat created this model for operations that need reliable performance without premium pricing. The "GC" might as well stand for "Gets the job Completed" - it handles the essentials without the cost of bells and whistles you might never use. The fuel efficiency makes a tangible difference in operating costs.
Caterpillar 966 GC
The 966 GC delivers premium performance with standard technologies that actually improve productivity rather than just adding complexity. It's the "right-sized" solution for operations that need more capability than the 950 but can't justify the full-featured 966.
Komatsu WA320-8
This consistent bestseller pairs 165 hp with 34,128-34,987 lbs operating weight and 3.0-4.2 cubic yard buckets - specifications that hit the versatility bullseye for general contractors. Prices from $137,500 to $267,000 reflect the wide range of hours and configurations available.
It excels in material loading, earthmoving, and those challenging digging operations where lesser machines start to struggle.
Komatsu WA270-8
Another Komatsu winner featuring 149 hp and 28,208-29,079 lbs operating weight with 2.5-3.5 cubic yard buckets. New units run around $230,000. What makes this machine special? Its balance of size, power, and agility that makes it productive across diverse applications rather than specialized for just one task.
Volvo L90H
Consistently on bestseller lists because it delivers premium performance with practical innovation. Tier 4f/Stage IV compliant with bucket options from 2.9 to 9.2 cubic yards and operating weight of 31,968-38,140 lbs.
New models price between $217,600-$257,975. Its versatility in agriculture, log handling, and waste management comes from engineering that focuses on cycle times and operator efficiency rather than just raw specs.
Caterpillar 966H
This proven performer continues earning its keep with 262 hp, 52,254 lbs operating weight, and 4.5-5.5 cubic yard buckets. Used pricing from $18,000 to $155,000 means there's one for practically every budget.
Construction, mining, and ag operations keep them in demand because they continue producing when flashier machines might be down for specialized maintenance.
Caterpillar 950 G
The 950 G maintains strong resale value despite its age - 197 hp, 39,203 lbs, 3.5-4.5 cubic yard buckets, priced used from $40,000-$82,000. Its reputation for handling punishing applications keeps demand steady in the secondary market where actual performance trumps model year.
Large Wheel Loaders
Caterpillar 994 & 994K
These mining machines move material at scales that make smaller loaders look like toys. When your operation measures productivity in hundreds of tons per hour, these purpose-built machines deliver what general-purpose equipment simply cannot.
John Deere 744 X-Tier
Deere's entry in the production class incorporates E-Drive (electric variable transmission) technology that delivers measurable fuel savings without sacrificing productivity.
With 325 hp and 56,524-59,267 lbs operating weight handling 5.0-5.85 cubic yard buckets, it's targeting aggregates and roadbuilding operations where fuel costs significantly impact profitability.
Comparison Table of Key Specifications and Costs
Model | Category | Engine Power (hp) | Operating Weight (lbs) | Bucket Capacity (cu. yd.) | Breakout Force (lbs) | Estimated Purchase Price | Common Applications |
---|---|---|---|---|---|---|---|
John Deere 324 P-Tier | Compact | 71 | 14,110 | 1.0–2.1 | 12,456 | $103,500 - $156,100 | Truck loading, bale handling, landscaping |
Caterpillar 908 | Compact | Not Specified | Not Specified | Not Specified | Not Specified | Not Specified | Contracting, landscaping, waste management, snow removal |
Bobcat L95 | Compact | 74 | 11,993 | 1.25 - 2.0 | Not Specified | $88,900 - $115,750 | Landscaping, nurseries, construction, agriculture, rental |
Komatsu WA320-8 | Medium | 165 | 34,128 - 34,987 | 3.0 - 4.2 | 31,151-44,287 | $137,500 - $267,000 | Material loading, earthmoving, pallet handling, hard digging |
Komatsu WA270-8 | Medium | 149 | 28,208 - 29,079 | 2.5 - 3.5 | 25,067-34,621 | ~$230,000 | Loading and handling in various conditions |
Volvo L90H | Medium | 184 | 31,968 - 38,140 | 2.9 - 9.2 | Not Specified | $217,600 - $257,975 | Agriculture, log handling, rehandling, waste handling |
Caterpillar 966H | Medium | 262 | 52,254 | 4.5-5.5 | 42,300 | $18,000 - $155,000 | Construction, mining, agriculture |
Caterpillar 950 G | Medium | 197 | 39,203 | 3.5-4.5 | 32,810 | $40,000 - $82,000 | Heavy-duty applications |
Caterpillar 994 | Large | Not Specified | 379,100 | 13.1-40.5 | 198,200 | Not Specified | Mining |
Caterpillar 994K | Large | 1,740 | 529,100 | 25-32.5 | 126,300 | Not Specified | Mining |
John Deere 744 X-Tier | Large | 325 | 56,524–59,267 | 5.0–5.85 | Not Specified | Not Specified | Aggregates, roadbuilding |
Versatility in Action: Applications and Usage Across US Industries
If wheel loaders could talk, their most overused phrase would be "I got this." These machines tackle an impressive spectrum of jobs that would make other equipment categories envious.
flowchart TD WL[Wheel Loaders] --> CON[Construction] WL --> MIN[Mining & Quarrying] WL --> AG[Agriculture] WL --> OTHER[Other Industries] CON --> CON1[Material Handling] CON --> CON2[Site Preparation] CON --> CON3[Material Transport] CON --> CON4[Light Excavation] MIN --> MIN1[Moving Earth & Overburden] MIN --> MIN2[Loading Haul Trucks] MIN --> MIN3[Managing Stockpiles] AG --> AG1[Stacking Hay Bales] AG --> AG2[Loading Feed & Grain] AG --> AG3[Transporting Supplies] AG --> AG4[Snow Removal] OTHER --> LAND[Landscaping & Nursery] OTHER --> WASTE[Waste Management] OTHER --> FOR[Forestry & Logging] LAND --> LAND1[Handling Mulch & Soil] LAND --> LAND2[Moving Plants] WASTE --> WASTE1[Handling Refuse] WASTE --> WASTE2[Sorting Materials] FOR --> FOR1[Moving Logs] FOR --> FOR2[Handling Woodchips] style WL fill:#f96,stroke:#333,stroke-width:2px style CON fill:#bbf,stroke:#333,stroke-width:1px style MIN fill:#fdd,stroke:#333,stroke-width:1px style AG fill:#dfd,stroke:#333,stroke-width:1px style OTHER fill:#ffd,stroke:#333,stroke-width:1px
Ever see a bulldozer try to load a truck? It's like watching someone eat soup with a fork - technically possible but painfully inefficient.
In construction, loaders are the ultimate utility players. One day they're moving material, the next they're prepping building pads, then they're placing pipe with precision that makes excavator operators nervous.
Their mobility lets them zip around sites where tracked machines would be tearing up finished surfaces and burning extra fuel. When infrastructure spending heats up, loader sales typically follow like clockwork - they're the canary in the economic coal mine for heavy equipment.
Mining operations don't just like large wheel loaders - they literally cannot function without them. We're talking about machines moving hundreds of tons per hour to keep haul trucks fed and production targets met.
A mine superintendent once told me, "Every minute my Cat 994 isn't loading is about $500 in lost production." These aren't just big machines; they're big money machines with specialized attachments like rock buckets designed for punishment that would reduce standard equipment to scrap metal within days.
Agriculture has embraced loaders with surprising enthusiasm. Dairy operations use compact models to handle feed and bedding materials with precision that old-school skid steers can't match.
Hay producers stack massive bales that would require three farmhands and questionable safety practices to move manually. The maneuverability and attachment versatility make these machines the Swiss Army knives of modern farming.
Beyond these primary uses, wheel loaders have become essential in specialty niches you might not expect. Landscape supply yards depend on their precision placement abilities - have you ever seen a skilled operator precisely load one scoop of mulch onto a half-ton truck without spilling a single piece? That's financial efficiency in action.
Waste transfer stations use specialized loaders with waste buckets where the alternative is handling materials nobody wants to touch twice. Forestry operations move logs and woodchips with machines that handle in hours what would take days with dedicated forestry equipment.
How many hours are these machines actually working? For general contractors, the sweet spot typically lands between 1,200-1,500 hours annually. Some Cat loaders log around 12,000 hours over a decade before major rebuilds - about 1,200 hours yearly of hard use.
Their engines often outlast the rest of the machine, with 8,000-15,000 hour lifespans being common. Interestingly, compact loaders typically see less annual use - Bobcat's extended warranty covers up to 6,000 engine hours over 5 years, suggesting they expect around 1,200 hours yearly for these smaller machines.
What does all this mean for buyers? Versatility has tangible value. A machine that can handle four different job functions might cost more upfront than a single-purpose unit, but the math on utilization rates and revenue generation makes the business case crystal clear.
That's why the loader - particularly in the mid-size range - remains the first heavy equipment purchase for many growing contractors.
From Innovation to Evolution: A Historical Perspective on Wheel Loader Technology
The wheel loader's journey from glorified farm tractor to technological marvel didn't happen overnight. Back in the 1920s and 30s, these machines were basically tractors with cable-operated buckets, using clutches for lifting and gravity (read: dropping) for dumping.
Imagine trying to perform precision material placement with that setup - it was about as elegant as performing surgery with oven mitts.
The 1940s brought the hydraulic revolution that changed everything. Suddenly, operators could actually control the lift and tilt functions with something resembling precision. This wasn't just an incremental improvement - it fundamentally transformed what these machines could accomplish and opened the door for the larger, more capable loaders we take for granted today.
Volvo deserves a tip of the hard hat for their early innovations. Their H-10 in 1954 featured a quick-attachment bracket that made implement changes dramatically faster - a concept so fundamental now that operators forget it was once revolutionary. This Swedish influence would continue shaping loader design for decades to come.
Articulated steering - that pivoting joint between the front and rear sections - represents another quantum leap forward. Mixermobile's Scoopmobile series introduced this concept in 1953, dramatically improving maneuverability in tight spaces.
Cat jumped on this train in 1963 with their 988A and 966B models, becoming early adopters of what would become industry standard.
Interestingly, John Deere came later to the articulated loader party - they introduced their first articulated motor grader (the JD570) in 1967, but their wheel loader line wouldn't get the same treatment until much later, with models like the 344L in 2018 offering rear-wheel steering for improved maneuverability.
The hydraulic systems themselves have evolved dramatically. Early Cat 966 models featured hydraulics that were advanced for their era but primitive by today's standards. Later iterations like the 966M incorporated significant design improvements that dramatically enhanced control and efficiency.
Volvo's OptiShift technology, introduced in 2011, was a genuine game-changer for energy efficiency - reducing fuel consumption by up to 15% in certain applications. Komatsu became an early champion of hydrostatic transmission (HST) technology, integrating electronically controlled HST into their WA series in the early 2000s, giving operators unprecedented control flexibility.
The digital revolution hit wheel loaders in the 1990s with the integration of electronic controls. Suddenly, machine operation became more precise, and fuel efficiency improved dramatically.
Today's machines feature sophisticated telematics like Bobcat's Machine IQ and Volvo's CareTrack that would seem like science fiction to operators from previous generations. These systems don't just track location - they monitor everything from fuel consumption patterns to hydraulic pressures, predicting maintenance needs before components fail.
Automation continues advancing from concept to reality. Cat's Command system has extended to medium wheel loaders, enabling remote operation in hazardous environments. John Deere's AutoDig feature takes the guesswork out of bucket loading, automatically optimizing the process for maximum efficiency while reducing operator fatigue.
Perhaps the most significant recent trend is the industry's pivot toward electric and hybrid power systems. Volvo has positioned themselves at the forefront, investing heavily in electric loader manufacturing and expanding their battery-powered lineup. LiuGong made headlines by selling their first battery EV wheel loader in the US market - a milestone that seemed improbable just five years ago.
John Deere joined the alternative power movement with their hybrid X-Tier production class loaders. Meanwhile, Komatsu's development of hydrogen fuel cell excavators signals where the broader industry might be heading - toward diverse power solutions tailored to specific applications and operating environments.
What's remarkable isn't just how far wheel loader technology has advanced, but how these innovations have made complex operations simpler for operators while simultaneously improving efficiency, reducing environmental impact, and extending machine longevity. The loader sitting on your jobsite today represents nearly a century of engineering evolution.
Market Dynamics: Analyzing US Wheel Loader Sales and Trends
The US wheel loader market isn't just healthy - it's showing the kind of growth that makes other equipment categories jealous.
Current projections indicate continued expansion in the coming years, with the compact segment particularly poised for significant growth. But what's actually driving this upward trajectory?
Infrastructure investment has emerged as the primary catalyst. When Washington opens the funding spigot for roads, bridges, and public works, wheel loader orders typically follow within 6-12 months.
The recent infrastructure package hasn't just created immediate demand - it's provided the multi-year project visibility that gives equipment buyers confidence to pull the trigger on fleet expansions. Alongside this, residential and commercial construction activity continues humming along at levels that keep material handlers busy and profitable.
Broader economic factors are playing their part too. Urbanization trends and population growth create an underlying demand floor that buffers against minor economic hiccups.
Meanwhile, technological advancements aren't just marketing fluff - they're delivering measurable improvements in productivity, fuel efficiency, and operator comfort that legitimately justify equipment replacements even when the old machine still runs just fine.
Speaking of replacements, the sales data between new and used equipment tells an interesting story. From August 2023 through July 2024, financing for new wheel loaders jumped 9.8%, while used equipment financing during the same period actually declined by 4%.
This suggests a shifting preference toward new equipment - possibly driven by improved features, warranty benefits, or changes in financing structures that make new machines more attractive relative to used options.
Despite this sales volume drop on the used side, prices for secondhand loaders climbed 6.6% during the same period.
This seemingly contradictory pattern likely reflects several factors: longer lead times for new equipment delivery making quality used machines more valuable, the general inflationary environment affecting all capital equipment, and perhaps a flight to quality as buyers focus on premium used machines rather than questionable specimens.
Regional variations in wheel loader activity paint a picture of America's economic geography. Texas, Florida, and Illinois topped the charts for new loader purchases, while Texas, New York, and Michigan led in secondhand acquisitions.
These patterns reflect both the obvious construction booms in growth states like Texas and Florida, but also the strong infrastructure renewal focus in established industrial states like Illinois, New York, and Michigan. Looking at broader regions, the North Central, South Central, and Northeast showed particularly robust market values in the used segment.
Two emerging trends worth watching: First, the growing emphasis on green building practices is creating demand for loaders with improved emissions profiles and fuel efficiency.
This isn't just environmental virtue signaling - projects with sustainability certifications often command premium prices, making the investment in cleaner equipment financially justifiable.
Second, the e-commerce explosion has dramatically increased warehousing and logistics activity, creating new demand centers for material handling equipment including appropriately-sized wheel loaders.
What does all this mean for buyers and fleet managers? The market fundamentals suggest continued steady growth rather than boom-and-bust cycles, which typically translates to stable pricing and reasonable lead times.
The increasing divergence between new and used equipment sales indicates that careful TCO (Total Cost of Ownership) analysis is more important than ever - the cheapest machine to buy rarely remains the cheapest to own over its operational life.
Conclusion: Navigating the Landscape of the Best Wheel Loaders
At its core, choosing the best wheel loader isn’t about brand loyalty—it’s about aligning capability with application. Cat, Komatsu, Deere, Volvo, and Bobcat all offer solid options, but the right machine for your operation depends on engine power, operating weight, bucket capacity, and breakout force. Equally important are long-term costs like fuel burn, maintenance schedules, and dealer support when breakdowns happen.
The industry is evolving, with infrastructure spending and technological advancements driving innovation. Hybrid and electric models are proving their worth, and telematics—once seen as a luxury—is now a key factor in reducing downtime and maximizing efficiency. These aren’t just trends; they’re reshaping how operators calculate ROI.
Ultimately, the perfect wheel loader for one job could be overkill for another. A model that boosts productivity for a quarry might be inefficient for a landscaping business. Smart buyers focus on total ownership costs, operational needs, and real-world performance—not just what looks good on paper.
FAQ
Which company loader is best?
The best loader company depends on specific needs, but Caterpillar, Komatsu, and Volvo are widely regarded for their reliability, performance, and advanced technology. Caterpillar is known for durability, Komatsu for innovation, and Volvo for fuel efficiency and operator comfort.
What is the life expectancy of a wheel loader?
The life expectancy of a wheel loader typically ranges from 7,000 to 12,000 operating hours. Proper maintenance and usage conditions can extend its lifespan significantly.
What is the most popular front-end loader?
The Caterpillar 950 series is one of the most popular front-end loaders due to its versatility, power, and efficiency. It is commonly used in construction, agriculture, and industrial applications.
Are New Holland wheel loaders good?
New Holland wheel loaders are considered reliable and efficient, offering good performance for medium-duty tasks. They are praised for operator comfort, ease of maintenance, and competitive pricing.